- Overview
- Product Description
Basic Info.
Model NO.
j522
Coating
Sodium silicate
Machining Tolerance
+/-0.01mm
Standard
ASME
Certification
CE, RoHS, ISO 9001:2000, ISO 9001:2008
Type
Dehumidifier
Application
Special Shapes
Fuel
Gas
Operating Pressure
Vacuum
Roller Number
Multi-Drum
Cloth Membrane Forms
Splash
Fluid Bed Drying Equipment Type
Horizontal Fluid Bed
Vacuum Drying Equipment Type
Continuous Vacuum
Condition
New
Color
Customized
Control System
PLC
Trademark
weltop
Origin
China
HS Code
8454309000
Production Capacity
5 Pieces/Month
Product Description
We are a leader in the foundry machinery industry with over 20 years of design and manufacturing experience. We can provide global customers with high-quality custom design, R&D, and manufacturing of foundry equipment, and have a perfect after-sales system.
We design and develop casting equipment for a wide range of industries. Cooperation with excellent customers has kept our technology in continuous progress, and the mechanical mechanism and automation level are constantly optimized and updated, helping customers improve production efficiency and product quality.
We have a professional technical team, including mechanical engineers, electrical engineers, mold engineers, and other professional technicians with rich experience. We rely on the progress of technology and the accumulation of experience, and constantly innovate and develop to provide quality casting equipment and services for our customers' environmentally friendly and efficient automated casting production.
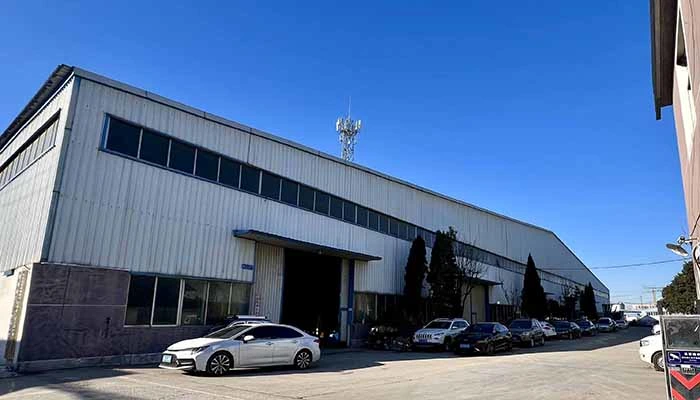
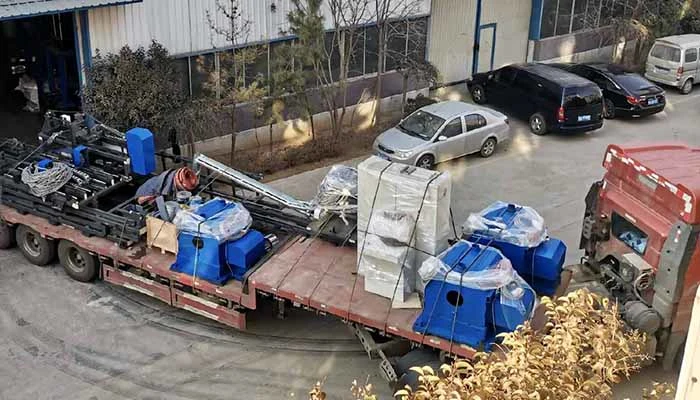
The double-station automatic servo-controlled cylinder sleeve centrifugal casting machine adopts the integrated structure of double main machines + multi-station auxiliary machines, with double main machines arranged side by side and controlled by frequency conversion. The double main machines share one set of auxiliary machine and casting devices. The auxiliary machine is controlled by a servo drive, which realizes the automatic control of the whole process of cleaning, spraying, pouring, cooling, pulling, and taking out the parts of the cylinder sleeve centrifugal casting production. The high speed and smooth speed adjustable main machine, advanced multi-stage and multi-speed spraying process, and real-time monitoring and adjustment of key process parameters in the whole casting process ensure the consistency of the casting process for each cylinder liner product, eliminate the influence of human factors on the casting process parameters, and fundamentally ensure the stability of the inner quality of the cylinder liner casting. The machine covers an area of less space, has high production efficiency, and needs only one person to operate. It is very suitable for the continuous production of single species and large quantities of cylinder liner blank castings.
Machine features:
High speed and smooth running of the main engine
Excellent spraying quality
Real-time monitoring of tube mold temperature and water spray cooling
Reliable casting taking out mechanism
Automatic pouring and accurate iron weighing
Efficient, safe, stable and flexible electrical automatic control system
Depending on the size of your castings and process requirements, let's work together to create a casting machine that better suits your needs.
If you need a more stable mechanism with a higher degree of automation, please contact us.
Technical parameters
Name | Values | Unit |
Casting diameter | Φ60~Φ120 | mm |
Casting maximum length | 1500 | mm |
Mold raceway diameter | Φ100~Φ180 | mm |
Riding wheel diameter | Φ300X70 | mm |
Two riding wheel outer span | 900 | mm |
The distance between ground and mold center | 800 | mm |
The host spacing | 800 | mm |
Speed of mold | 0~2000 | rpm |
Centrifugal machine power motor | 7.5 | Kw |
Pulling car power | 2.2 | Kw |
Cleaning car power | 0.37 | Kw |
Praying car power | 0.4 | Kw |
Mobile platform power | 1.0 | Kw |
Pouring car power | 1.0 | Kw |
Pouring ladle power | 0.4 | Kw |
Pouring ladle turning power | 0.75 | Kw |
Pulling stroke | ≥2200 | mm |
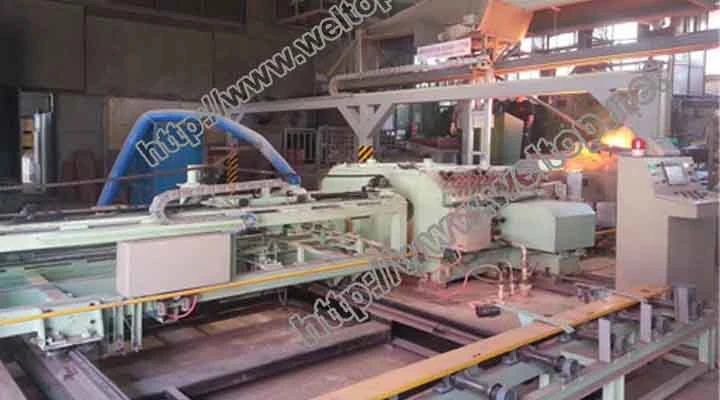
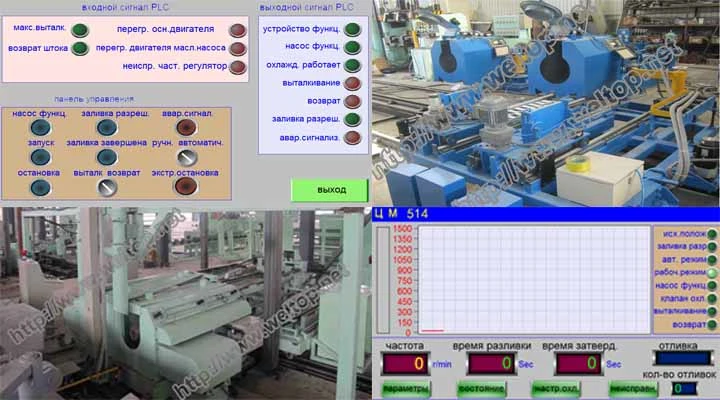
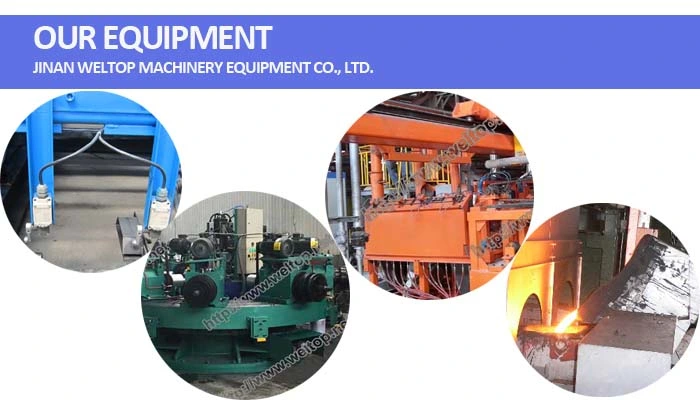
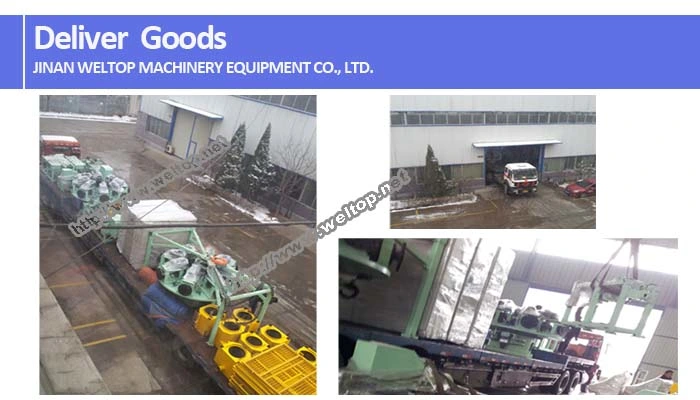